Summary:Floating ball valves have emerged as versatile and reliable solutions for fluid control in a wide range of industries. These valves offer excellent sealing capabilities, efficient flow control, and ease of maintenance, making them indispensable compo......
Floating ball valves have emerged as versatile and reliable solutions for fluid control in a wide range of industries. These valves offer excellent sealing capabilities, efficient flow control, and ease of maintenance, making them indispensable components in numerous applications. From oil and gas to chemical processing and water treatment, floating ball valves play a crucial role in ensuring the smooth operation of fluid handling systems.
The design of floating ball valves features a hollow ball with a floating structure. When the valve is in the closed position, the pressure of the fluid pushes the ball against the valve seat, creating a reliable seal that prevents leakage. As the valve handle or actuator is turned, the ball rotates, allowing the fluid to flow through the open pathway. This design offers low torque operation and excellent sealing performance, making floating ball valves ideal for applications that require precise flow control and tight shut-off capabilities.
One of the key advantages of floating ball valves is their versatility. These valves can handle a wide range of fluids, including liquids, gases, and even slurries. Their ability to accommodate different types of media and withstand varying temperatures and pressures makes them suitable for diverse industries. Floating ball valves are commonly used in oil and gas production, refineries, chemical plants, power generation facilities, and water distribution networks.
In the oil and gas industry, floating ball valves are critical components in upstream, midstream, and downstream operations. These valves are commonly used in pipelines, storage tanks, and processing facilities to control the flow of crude oil, natural gas, and petroleum products. Their reliable sealing properties and resistance to harsh operating conditions ensure safe and efficient transportation and processing of hydrocarbons.
Chemical processing plants heavily rely on floating ball valves for precise flow control and isolation of corrosive or hazardous fluids. These valves are designed to withstand aggressive chemicals and high temperatures, offering excellent resistance to corrosion and erosion. Their reliable shut-off capability minimizes the risk of leaks or spills, protecting both personnel and the environment in chemical manufacturing processes.
Water treatment and distribution systems also benefit from the use of floating ball valves. These valves help regulate water flow, ensuring efficient water management and distribution. The ability to provide a tight seal prevents water loss, reduces energy consumption, and helps maintain water quality. Floating ball valves are widely used in municipal water supply networks, wastewater treatment plants, and irrigation systems, contributing to the efficient use and conservation of water resources.
Maintenance and repair of floating ball valves are relatively straightforward, adding to their appeal. The ability to access and replace the ball and seats without removing the entire valve from the pipeline minimizes downtime and reduces maintenance costs. This feature is particularly advantageous in industries where uninterrupted operation is crucial, such as power generation and oil refineries.
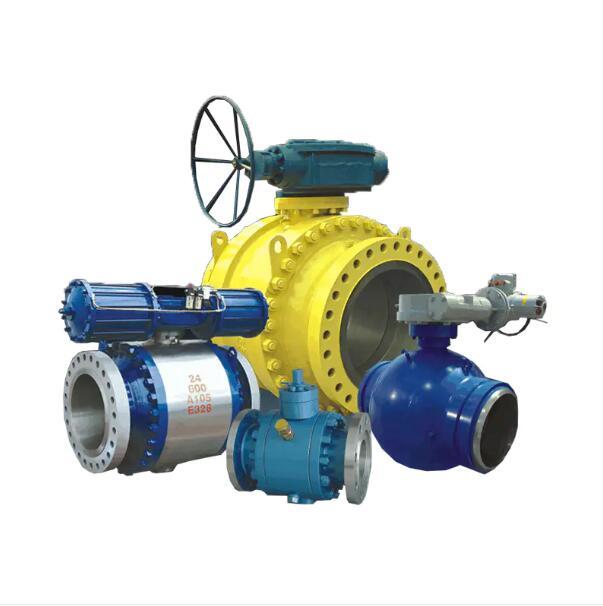