Summary:Floating Ball Valves are used to control the flow of liquids and gases in pipelines and other piping systems, both in industrial and commercial environments. They can be operated manually, by a lever, gear or pneumatic/hydraulic device. They can also......
Floating Ball Valves are used to control the flow of liquids and gases in pipelines and other piping systems, both in industrial and commercial environments. They can be operated manually, by a lever, gear or pneumatic/hydraulic device. They can also be automated. They can stop, distribute and alter the direction of liquids’ flows within a system while providing a reliable seal in both directions.
There are two major subtypes of a floating ball valve; two-piece and three-piece. Both are designed to meet a range of working conditions, including high temperature and pressure. The most common is the two-piece version. This is the less expensive of the two and is most often used in situations where space is an issue. Three-piece versions are more expensive than the two-piece model but they offer an improved performance in terms of resilience and sealing capabilities and can be used in a wide range of applications, including critical high-pressure operations.
Both types work in a similar way; when the valve is closed the onstream pressure pushes the upstream seat and the ball to the downstream seat creating a seal. The main difference between the two is that in floating ball valves the seats require a separate mechanism to release additional pressure while in trunnion mounted ball valves the seats are self-relieving.
One of the biggest issues in a floating ball valve is the seating material, which is typically made from some form of thermoplastic, such as PTFE. These materials are soft enough to provide a reliable seal against the highly polished metallic ball but they must be able to hold up under the pressure applied by the in-line fluids. This means that the seats must be able to deform slightly as the temperature and pressure changes, while at the same time remaining rigid enough to prevent any leaking.
Resilient-seated floating ball valves are able to overcome these challenges by adding a layer of metal on top of the elastomeric seat. The layer of metal acts as a backup in the event that the elastomeric seat fails. This allows resilient-seated floating ball valves to perform reliably in high-pressure and high-temperature applications that would normally be unsuitable for other valve designs.
Whether you choose to go with a resilient-seated or hard-seated floating ball valve, there are still a number of other variables that will influence the type of valve you ultimately select. The material, size, and operating temperature of your application will all play a part in deciding which style of valve is right for you.
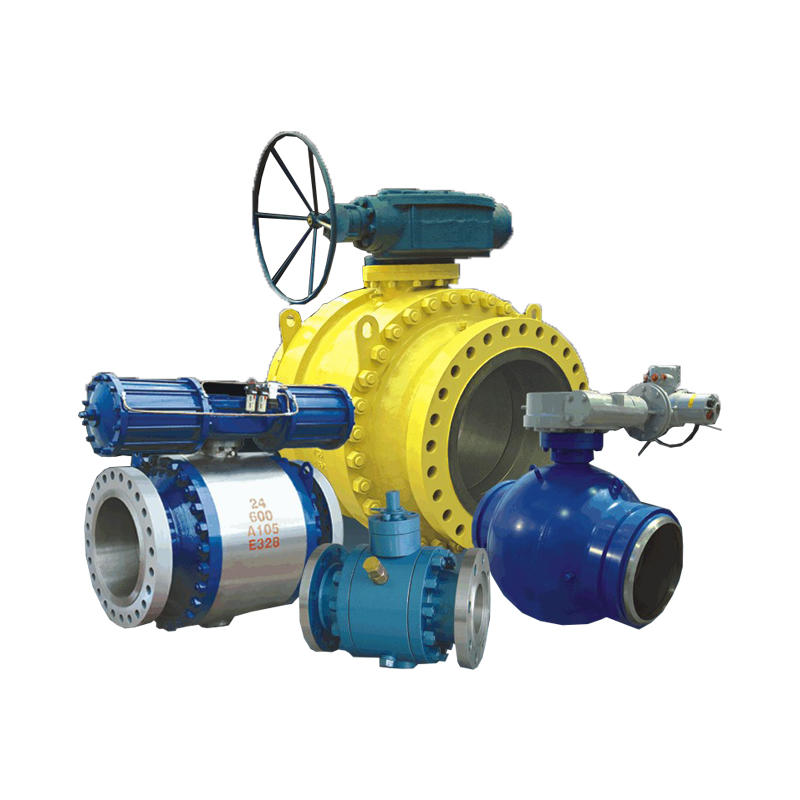