Summary:
Forged steel valves, cast iron valves, and stainless steel valves are vital components in fluid control systems, each with unique characteristics and applications.
Forged Steel Valves: Forged steel valves are manufactured by heating and hammering ......
Forged steel valves, cast iron valves, and stainless steel valves are vital components in fluid control systems, each with unique characteristics and applications.
Forged Steel Valves: Forged steel valves are manufactured by heating and hammering or pressing steel billets. The forging process imparts a dense and uniform internal structure to the valves, resulting in high strength and pressure-bearing capabilities.
Cast Iron Valves: Cast iron valves are formed by pouring molten iron into molds, followed by cooling and solidification. While cast iron valves have lower production costs, their strength and pressure-bearing capabilities are typically lower than forged steel valves.
Stainless Steel Valves: Stainless steel valves are made from stainless steel materials known for their excellent corrosion resistance and mechanical properties. Stainless steel valves are produced through casting or forging processes, offering a balance between strength and corrosion resistance.
Forged Steel Valves: Due to their forged construction, forged steel valves exhibit high strength and pressure-bearing capacity. They are suitable for high-pressure and high-temperature applications, providing reliable performance under demanding conditions.
Cast Iron Valves: Cast iron valves have relatively lower strength and pressure-bearing capabilities compared to forged steel valves. They are typically used in low-pressure or general applications.
Stainless Steel Valves: Stainless steel valves offer moderate pressure-bearing capacity, suitable for medium-pressure applications or corrosive environments where corrosion resistance is critical.
Forged Steel Valves: While forged steel valves may offer good corrosion resistance, they are not as corrosion-resistant as stainless steel valves. Depending on the specific alloy used, forged steel valves may require additional protective coatings or treatments to enhance corrosion resistance in corrosive environments.
Cast Iron Valves: Cast iron valves are susceptible to corrosion, especially in highly corrosive environments. They may require corrosion-resistant coatings or linings to prolong their service life in such conditions.
Stainless Steel Valves: Stainless steel valves are renowned for their excellent corrosion resistance, making them ideal for applications involving corrosive fluids or environments. They are resistant to rust, oxidation, and chemical corrosion, ensuring long-term reliability in harsh conditions.
Forged steel valves, cast iron valves, and stainless steel valves offer distinct advantages and considerations in terms of materials, pressure-bearing capabilities, and corrosion resistance. Forged steel valves excel in high-pressure and high-temperature applications, cast iron valves are suitable for low-pressure or general applications, while stainless steel valves are ideal for corrosive environments. Understanding the differences between these valve types is crucial for selecting the most suitable valve for specific applications, ensuring optimal performance and reliability in fluid control systems.
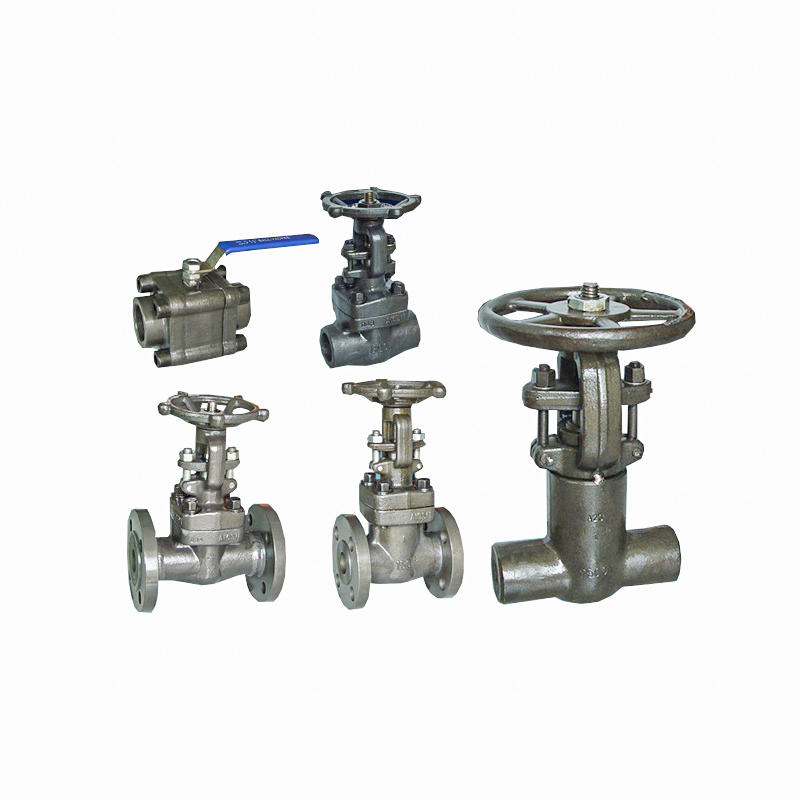