Summary:Ball valves are commonly used to control the flow of water, oil, gas and other compatible fluids. They can be used to stop and start the flow, increase or decrease the amount of flow, or control the pressure of a process. A ball valve has four main p......
Ball valves are commonly used to control the flow of water, oil, gas and other compatible fluids. They can be used to stop and start the flow, increase or decrease the amount of flow, or control the pressure of a process. A ball valve has four main parts: the valve body, a central metal ball, the seating that holds the ball within the duct opening (port), and the stem that connects the seat to external controls. The valve stem can be rotated to open and close the valve, either manually with handles or levers or automatically through actuation such as electric, pneumatic, or hydraulic power sources.
Valves come in a variety of shapes, sizes and materials. The most common type of valves are made from stainless steel, brass, or nickel-plated brass, PVC, or a similar tough plastic polymer. Brass is an excellent choice because it has good corrosion, rust, and oxidation resistance. It also has antimicrobial properties that prevent the growth of bacteria and other microbes.
Valve bodies are designed in two types: one-piece and multi-piece. One-piece valves are relatively inexpensive but can be difficult to repair. Multi-piece valves, on the other hand, are typically more expensive but can be easily repaired and disassembled for cleaning or repairs.
The seats that hold the ball are built in a specific design to ensure the valve is seated correctly, and there is no leakage when the valve is closed. Seats can be reduced or full port; reduced port valves are the most common. Full port valves have a larger bore diameter than the pipe and provide fewer friction losses, but can be more costly to manufacture.
A valve's packing is a flexible seal that fits around the stem to keep the media inside the piping system and not outside. The packing can be elastomeric, rubber or a combination of both. It can also be soft or hard, depending on the needs of a specific application.
The stem of a valve is what connects the internal ball to the external control device. This can be a handle or lever that an operator manipulates, or it can be an automated power source such as electric, pneumatic or hydraulic. The actuator must be able to move the stem of the valve quickly and accurately in response to changing signals from an operator. If a valve is manually operated, high levels of accuracy will cause the partially exposed elastomer seat to wear, leading to leakage and poor performance.
Often, these leaks are caused by dirt or residues that can build up in the cavity between the seat and the valve's body. In some cases these residues are a health hazard, and in others they can lead to cross-contamination of different liquids. Regular cleanings are essential for preventing these problems and keeping the valve in good working order. The best cleaning agents for valves are water or alcohol-based cleaners that don't react negatively with the metal or non-metal parts of a valve.
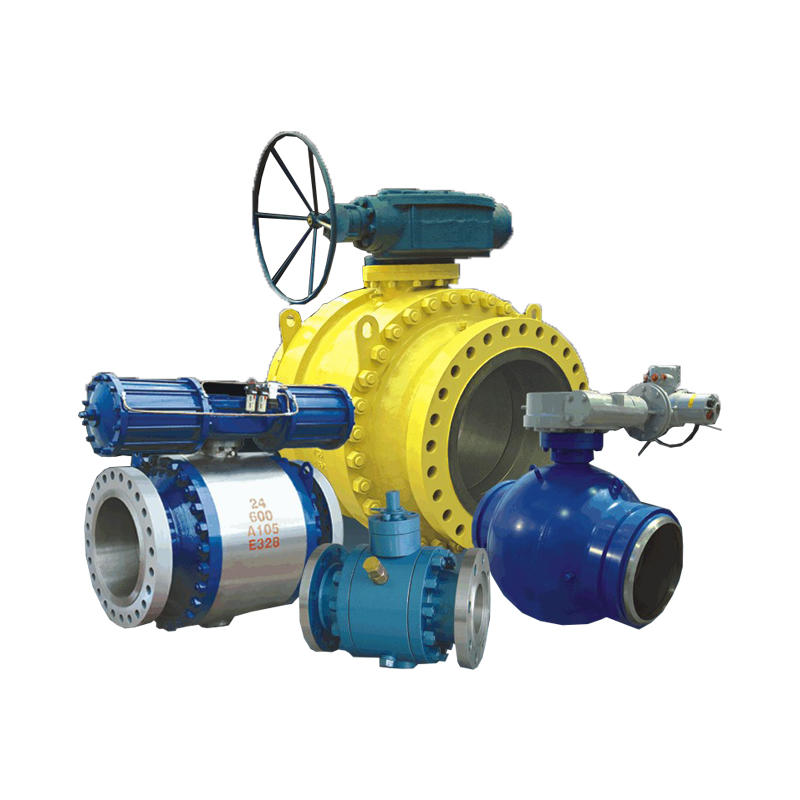